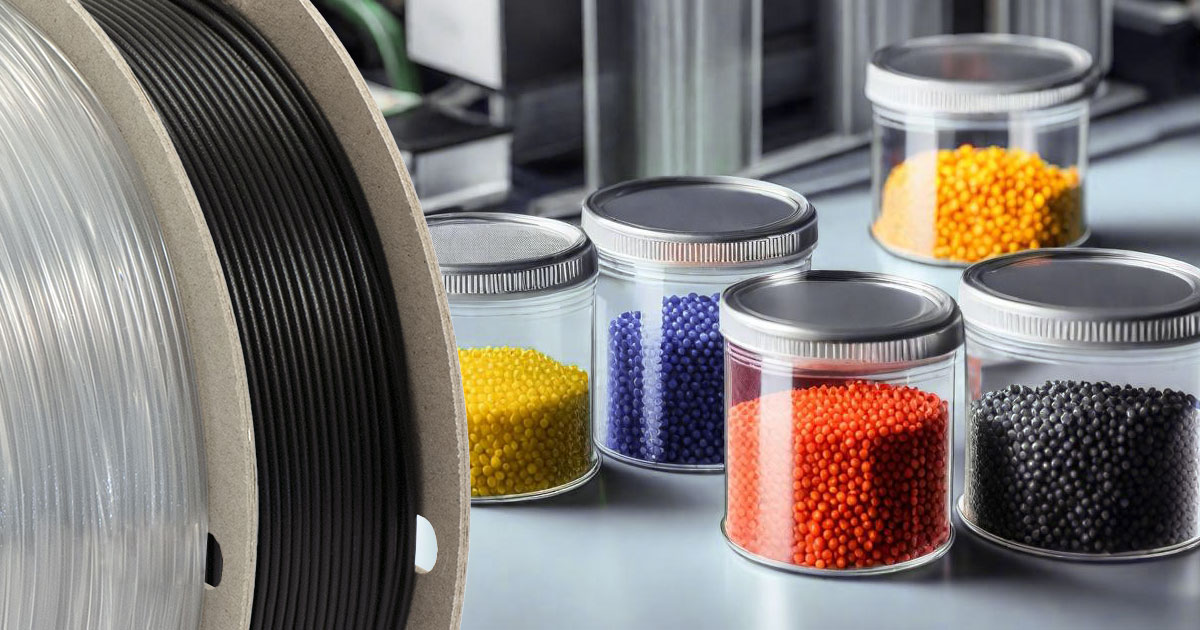
Is there a difference between natural and black?
We are often asked whether there is a difference between natural and black colors in 3d printing and the use of printed parts.
When it comes to filaments, there is a difference. Yes, provided that the inks are selected for the chosen polymer, and the ink manufacturer fights for quality and does not save on materials, this difference will be insignificant, about 5-7%, and often it does not significantly affect the printed product. However, if you have sufficiently accurate calculations of the part regarding its operation in the finished project (system) and 5-7% can interfere with this work, then you should take a more detailed approach to choose the color for the plastic you have chosen for printing or select another plastic with a more significant safety margin, for example, or with the properties you need.
Of course, plastics without added colors will work best, or, as the manufacturer often indicates, the natural color. According to publicly available research, black plastics are the next best. The fact is that black pigments are made from components that include soot. It is the filler that strengthens the polymer. Depending on the structure of the soot, such paints can even improve the properties of the polymer in terms of strength, but you should not emphasize this and take this property into account if you do not have a clear answer from the manufacturer. And then there are all the other colors. We haven’t found any studies that show the dependence of plastic characteristics on a specific color, but the strength tests we have done with our filament have shown approximately the same results for all the other colors in our range.
Here are some other thoughts we would like to share when choosing a color:
- Some additives can significantly degrade the performance of colored plastics. If the filament manufacturer does not conduct special studies on the interaction of additives with inks for a particular plastic, you should choose either natural or black filament colors from this range.
- The properties of colored plastics are strongly influenced by the production process of the filament itself. For example, extrusion parameters for the same plastic but with the addition of different inks can be quite different. There may also be a situation when the equipment is not suitable for high-quality mixing of inks with plastic. The latter is scarce, but if you use some complex engineering polymers or very exotic colors, the properties of the finished part may differ from the usual 5-7%.
- The same color can be obtained using pigments that are fundamentally different in nature. This is to say that the same filament color may have different properties from different manufacturers. Usually, the manufacturer does not disclose this information, although some technical documents, such as SDS, contain such information. You should not compare green ABS from one manufacturer with green ABS from another. You should start with basic tests, such as a temperature tower.
And if you don’t have precise requirements for the finished part, then the choice of color is a personal preference.
Let’s continue our conversation about how paints affect polymer properties. Today we will talk about resins.
The most significant difference with filaments is that inks do not affect the mechanical properties of printed parts. More precisely, they do, but in the same way for everyone. And this influence can only be studied theoretically. The fact is that the resin (we will use the term “system” hereafter) does not work without the addition of inks. Hence, it is impossible to check the properties before and after the addition, or rather after, but there is nothing to compare it with. Yes, there are transparent photopolymer resins, but this system is developed with other components with the addition of several additives that stabilize this system and make it suitable for printing.
So, in theory, the inks added to the resins affect the final properties of the parts printed from these resins. And, again, in theory, these dyes worsen the properties of the system in general. But since the system does not work without adding paints, we accept this as a prerequisite. All the tests that show us the real properties of the polymer, in this case, are carried out with the finished system, so you can safely take the technical data (which the manufacturer usually provides in the technical documentation for the resin, for example, in the TDS document) for calculations in your projects.
Only one thing can be affected by the colorant in a ready-made system – the printing parameters. Indeed, for the same resin, the parameters can differ depending on the color. This is due to the different
reactivity of dyes – some can cure faster in the UV, and some take a little longer. As for post-processing, the manufacturer’s recommendations are usually general. In the case of photopolymer resins, a longer time of additional lightening after printing will not worsen the properties of the part, so these recommendations are usually given with a margin in case a particular color requires a little more time for additional lightening.
And don’t forget to shake the resin well before printing. The point is that the dye particles can settle over time, and before printing and, most importantly, during printing, it is necessary to ensure that the distribution of these particles is as uniform as possible. During the printing process, the raising and lowering of the table is responsible for this, which leads to the mechanical stirring of the resin. Before printing, you should take care of this yourself.