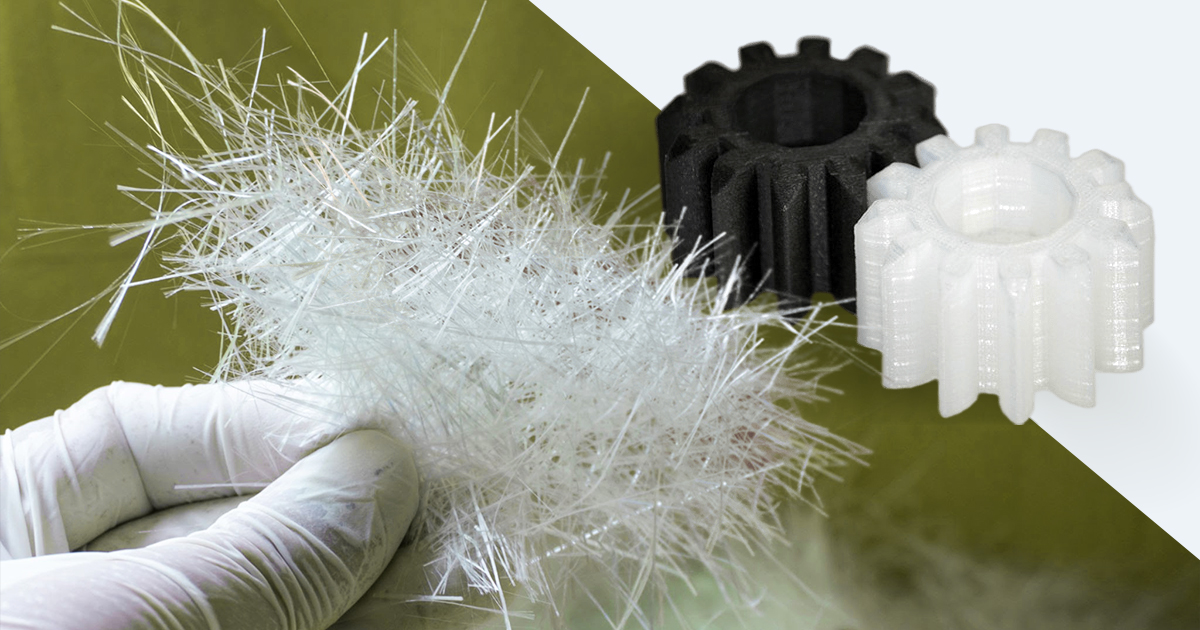
Fillers for 3D printing filaments and their properties
For many engineering applications, polymers are often modified by adding various additives. Filaments can also be filled with different fillers and modified with additives to make them more suitable for complex applications where the properties of a standard polymer are not quite suitable. Let’s look at what additives and additives exist and how they affect the properties of the finished model and the printing modes.
Conventionally, everything that can be added to the filament can be divided into three groups:
- Additives that enhance the current properties of the polymer
- Additives that add properties to the polymer
- Additives modify the properties of the polymer, making it different from its original form.
All of these additives and fillers are added during the filament extrusion process, thus. Yes, there is nothing new chemically, except for some structural changes in the case of the additive group, which change the very properties of the polymer. The most important thing in the technological process here is to get the right mixture of polymer and additive. Then all the new properties will be fully realized. For this purpose, there are special extruders; more often, they are twin-screw lines that work first of all as mixers. The output of such work is a new pellet from which filament is produced. Some additives can be added directly during the filament production process. But these subtleties are beyond the scope of this article, so let’s move on to the additives themselves.
So, above, we have conditionally categorized additives into groups. Let’s see what additives there are in each group and how they affect the properties of polymers.
The first group often includes solid fibers, the role of which is to strengthen the polymer, and as a consequence, higher strength characteristics of the printed model. Fibers are often fillers made of glass, carbon, or other fibers. They can be added to increase the strength and stiffness of printed products. They can also improve tear resistance (carbon fiber), wear resistance (Teflon), and improve impact resistance (glass filler). It is rare for more than one type of fiber to be used simultaneously, as any fiber affects several strength properties at once. Depending on the characteristics of the fiber itself, such as particle size, we can vary the physical values. But for 3D printing, we have quite strict limitations, primarily related to the layer size, when setting printing parameters. Hence, frankly speaking, we have a rather limited increase in strength values. However, this does not prevent the production of such filaments, as there is a vast range of tasks that are not solved by conventional filaments, but filled with carbon fiber, for example, solved in excess. It should be noted that such additives usually have a terrible effect on printers, which leads to frequent nozzle changes and additional maintenance of the printer. As for temperature characteristics, there are specific changes here, but they are not critical. If your printer can print with regular nylon, it can print with carbon fiber.
Examples of non-standard or unusual fillers include cellulose, which will give the filament the appearance of wood. The physical characteristics of the fleece are slightly older, cellulose has no strengthening effect as such, but it has a positive effect on shrinkage, making it smaller, and also improves adhesion.
As an example, I would like to talk about nano-diamond. This additive can be an abrasive, if the particle fraction is more than 4 microns and have the exact opposite properties if the fraction is less than 4 microns. Moreover, diamond particles improve mechanical properties such as strength modulus, making the material more stress-resistant. Plexiwire has used such an additive in producing its filaments and plans to renew and expand this product line.
Moving to the second group of additives, we would like to note that here we will talk about specific properties that are not related to the direct properties of the polymer, but are necessary to solve specific problems where pure polymer does not work. There are a huge number of such additives. Here are some frequently used examples:
- Metallic particles: Adding metallic particles such as aluminum or stainless steel can give printed products a metallic appearance and properties such as thermal conductivity or magnetic properties.
- Ultraviolet (UV) stabilizers: UV stabilizers are added to increase the resistance of printed products to ultraviolet radiation, preventing fading and degradation in the sun.
- Lubricating additives: Adding lubricating additives such as polyethylene or polytetrafluoroethylene (PTFE) particles can improve slip and reduce friction in printed products.
- Supersonic Additives: These additives accelerate print speeds, allowing faster printhead movement in the X, Y, and Z axes.
- Antimicrobial additives: Adding antimicrobial agents can prevent the growth of bacteria and fungi on printed products, which is helpful for medical and other applications where hygiene is important.
As well as additives that prevent the polymer from burning, odorizing it, conductive additives, etc. Indeed, the list of such additives is enormous, and often, they work perfectly with a wide range of polymers.
The third group is the most complex because the task of such additives directly changes the properties of the polymer. Such additives include additives that can make a tough polymer soft, or vice versa, change the structure from crystalline to amorphous, and additives that can reduce or eliminate moisture absorption.
The most famous example in 3D printing is PETG, where the base material is polyethylene terephthalate (PET), and the modifier is glycol. This modifier changes the crystalline structure of PET to amorphous, thus changing the properties of the polymer. Another example is ABS+, a classic example of this group of additives when the additive is introduced directly in the filament production process.