ABS CF 10
Plexiwire ABS CF 10 is the newest addition to Plexiwire’s Carbon filled filament series. This material combines the benefits of standard ABS with adding carbon fibers, often called “carbon.” With a 10% chopped carbon fiber content, the printed parts offer increased tensile and compressive strength. CF provides excellent adhesion between layers and minimizes shrinkage. Carbon fibers, also known as “Carbon,” contribute to product geometry stability by reducing thermal expansion, reducing warpage, and evenly distributing mechanical loads.
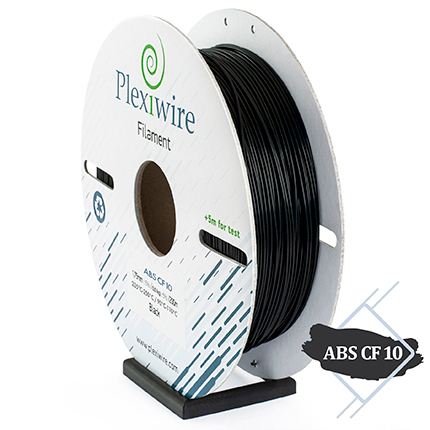
ABS CF 10 is:
- Enhanced strength - with the addition of carbon fibers, the power of the material is significantly increased, making it ideal for even more demanding engineering challenges.
- Dimensional stability - carbon fibers reduce the coefficient of thermal expansion, making the product less likely to deform as temperatures change.
- Excellent layer adhesion - carbon fiber ABS provides better adhesion between print layers, improving the appearance and strength of the product.
- Less shrinkage - thanks to the carbon fibers, shrinkage of the material after printing is minimized, allowing the exact dimensions of the product to be maintained.
- Ease of processing - despite its enhanced strength, carbon fiber ABS is still relatively easy to process, allowing for additional finishing or modification of printed parts.
- Reduced warping effects - carbon fibers prevent the material from bending and warping during printing, which is especially important for large parts.
Characteristics of PLexiwire ABS CF 10 Filament
- extruder temperature
- 235°С - 250°С
- platform temperature
- 90°С - 110°С
- print speed
- 40 - 65 mm/s
- Diameter
- 1.75mm
- Size
- 100 / 200 meters
- weight
- 0.25 / 0.5 kg
Colors:
- Black
Recommendations
- Nozzle and table temperature: For carbon-filled ABS, it is recommended to set the nozzle temperature between 250-270°C and the table temperature around 100°C. The high temperature ensures optimal adhesion of the layers and reduces the possibility of warping.
- Careful with blowing: The material can be sensitive to sudden temperature changes due to the addition of carbon fibers. Therefore, minimizing blowing or turning it off thoroughly is recommended to prevent rapid cooling and cracking.
- Additional Adhesives: To ensure maximum adhesion of the first layer to the print bed, specialized adhesives are recommended. They will help prevent the peeling and warping of the model, especially with larger print sizes.
- Use specialized nozzles: If you plan to print with carbon-filled ABS frequently, it is recommended that you equip your 3D printer with nozzles made of wear-resistant materials such as hardened steel. The carbon fibers in the filament are abrasive and can cause standard brass nozzles to wear out quickly.